Pad Printing vs UV Printing: Which Offers Better Results?
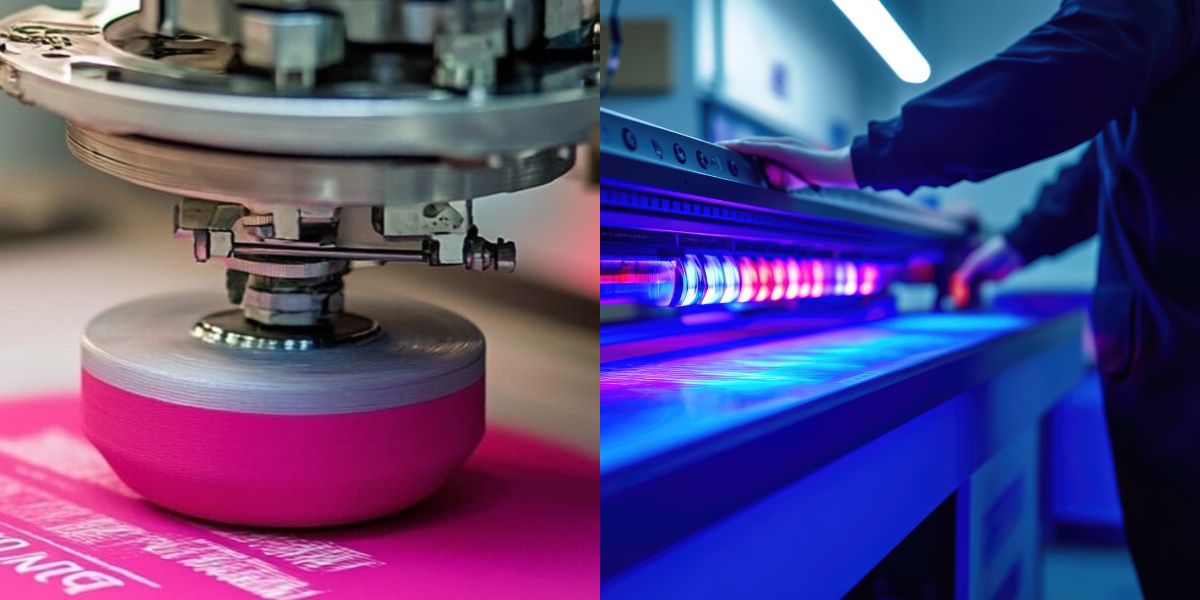
Pad printing and UV printing are now 2 popular techniques widely used for their ability to create durable and handle small, detailed prints. However, do you know which is more suitable with your printing projects?
To make the right choice, keep reading our article. We from CustomAny, will explain about each in the battle of “Pad printing vs UV printing”, guiding you through the key similarities and differences between them.
Getting started
First, let’s learn about pad printing and UV printing to know what they are.
What is Pad Printing?
Pad printing is also known as tampography or tampo printing. In this technique, ink is transferred from etched plates (also called clichés) onto products with a flexible silicone pad.
Pad printing is ideal for printing intricate details and high-quality images on small items. Although it is effective on flat surfaces, this printing truly excels in handling products with irregular shapes.
We’ve rounded up all the important things about Pad printing in our previous blog post. Read it here.
What is UV Printing?
UV printing is a digital printing process that utilizes ultraviolet lights to instantly dry or cure the ink as it’s applied to the material. As the printer lays down the ink, UV lights immediately follow, curing the ink for a quick and efficient finish.
With UV printing, the low curing temperatures allow for printing on even heat-sensitive materials. Therefore you can use this method for items made from wood, glass, ceramic, leather, canvas, metal, and a variety of plastics.
Fact: UV printing is the printing method we’re using to produce our best seller sticker product: UV DTF transfer stickers.
Pad Printing and UV Printing: What they share in common
Pad printing and UV printing share several key characteristics that make them versatile and widely used in various industries:
1. Multiple material compatibility
The inks of pad printing and UV printing have a great adaptability and they can accommodate different materials.
This wide material compatibility makes both pad printing and UV printing ideal for various materials, including:
- Plastics
- Metals
- Glass
- Ceramics
- ….
2. Able to print small, intricate items
Both pad printing and UV printing can handle small, detailed prints.
Pad printing achieves this through the use of fine plates and precise pads that can accurately transfer intricate designs.
On the other hand, UV printing offers high-resolution output because it uses high-precision mechanisms and its UV light cures the ink instantly without fading or blurring.
The UV printing process can add depth or texture to printed objects, which helps to achieve raised effects on small surfaces without losing details.
Pad Printing vs UV Printing: Key differences you must know
In the next step of considering “pad printing vs UV printing“, Once finding out the similarities between them, here are their distinct differences you must know to pick out the more suitable printing method:
Aspect | Pad Printing | UV Printing |
Printing process | Indirect transfer using silicone pad | Direct digital printing with UV curing |
Surface compatibility | Ideal for uneven, curved, and textured surfaces | Ideal for surfaces that are flat or slightly curved |
Durability | Requires additional coatings for durability | Highly resistant to fading, scratches, and environmental conditions |
Speed of production | Slower due to manual setup and handling | Faster with instant curing and minimal setup |
Cost | Higher setup costs, economical for large runs | Higher initial costs, economical for short runs |
Printing process
“Pad printing vs UV printing“? They differ fundamentally in their processes. Pad printing process involves an indirect transfer method where ink is picked up by a silicone pad from an etched plate. Then, it is transferred onto the object.
In contrast, UV printing is a method that uses UV light to cure the ink immediately upon printing, creating an instant drying effect.
Surface compatibility
One of the significant advantages of pad printing is its ability to print on irregular surfaces. The flexible silicone pad can conform to different shapes, ensuring even ink transfer.
UV printing, however, is generally more suitable for flat or slightly curved surfaces. Its best results are achieved on materials where the printhead can maintain a consistent distance for image clarity and precision.
Durability
Pad printing often requires additional coatings to enhance durability, especially when used on products that will be exposed to wear, chemicals, or harsh environments.
UV printing, on the other hand, produces prints that are durable due to the UV curing process, which bonds the ink to the substrate. UV prints like our 3D UV transfer labels are resistant to fading, scratches, and many environmental conditions.
Speed of production
Speed is a critical factor when you decide between pad printing vs UV printing.
Pad printing tends to be slower due to the manual steps involved in setting up:
- Plates
- Inks
- Pads
In contrast, UV printing, with its instant curing process, allows for faster production speeds, reducing the overall time. This makes the UV printing machine more efficient for short-run or time-sensitive projects.
Cost
The pad printer has higher initial setup costs due to the need for custom plates and pads. So, it is more economical for large-volume runs where these costs can be amortized over many units.
Conversely, UV printing, while having a higher initial investment in equipment, is cost-effective for short runs or on-demand printing.
Pad Printing vs UV Printing: Choose the best method for you project
Now you know the similarities and differences between pad printing and UV printing. Here are our quick guide to help you select the right printing method matching your requirements:
When to Use Pad Printing:
1. Printing on irregular or curved surfaces
Pad printing is ideal for objects with complex shapes, textures, or curves, such as pens, balls, toys, or industrial components. The silicone pad adapts to these surfaces, ensuring accurate ink transfer.
2. Small to medium-sized runs
If your project involves small to medium-sized runs, especially with intricate details on varied materials, pad printing can be cost-effective and versatile.
When to Use UV Printing:
1. High-volume production
UV printing is excellent for high-volume projects due to its fast production speed and minimal setup time.
2. High-resolution and vivid colors
For projects requiring vibrant, full-color images with high resolution, UV printing delivers superior quality with immediate curing, producing sharp and detailed prints.
3. Outdoor or high-durability needs
UV prints are highly resistant to fading, scratches, and harsh environmental conditions. This makes them perfect for outdoor applications or items that demand durability, such as labels or outdoor signs.
Wrap it up
In conclusion, when compare “pad printing vs UV printing“, we knew that they offer similar and distinct advantages for your project. Pad printing is ideal for irregular, curved surfaces and small to medium runs, while UV printing excels in high-volume production, delivering vivid colors and high durability.
We hope that our article can help you pick out the more suitable printing method for your needs between these two.
For more useful information about printing techniques and other printing tips, visit our website and check out our other blogs about printing!
FAQs
1. Which printing method is better for high-resolution graphics?
UV printing is the superior choice for high-resolution graphics, as it delivers vibrant, detailed images with excellent color fidelity and sharpness.
2. Can pad printing be used for outdoor applications?
You can use pad printing outdoors. However, this method often requires additional protective coatings to improve its durability and resistance to environmental elements.
3. Pad printing and UV printing – Which method is more cost-effective if I just need small production runs?
The flexibility of digital printing and the low setup costs of UV printing make them more economical for small production runs. This technique is ideal for short runs without the need for extensive preparations.
4. How does setup time compare between pad printing and UV printing?
Pad printing generally involves a longer setup time, particularly when multiple colors are involved. For each color, there’s the need for custom plates and pads.
Contrary to this, UV printing offers quicker setups with instant ink curing, making it much faster for production.