What is Flexographic Printing? Pros & Cons and Its Best Applications
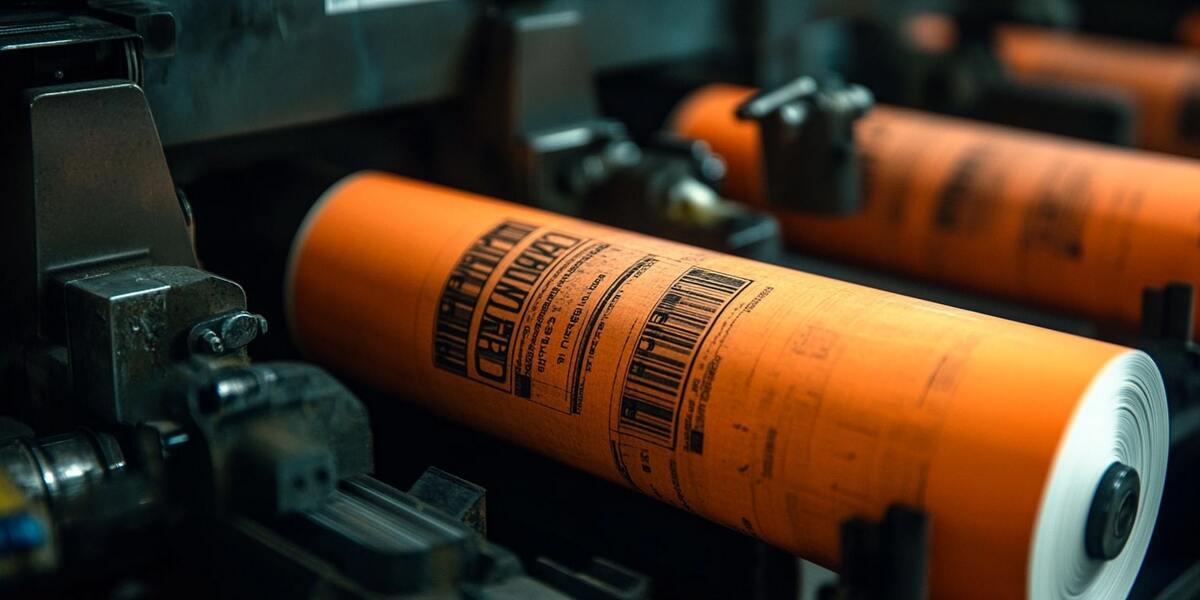
Flexographic printing is a versatile and widely-used printing technique, especially popular for producing high-quality labels, packaging, and more.
In this blog post, CustomAny will break down what flexographic printing is, explore its advantages and disadvantages, and highlight the best applications for this technology. Once learning about this printing method, you can decide if flexo printing is the right choice for your needs.
About Flexographic printing
What is Flexographic Printing?
In fact, flexographic printing (or flexo printing) is a modern version of the traditional letterpress technique. It uses flexible relief plates made of rubber or photopolymer. These plates have raised images that transfer ink onto a variety of substrates, including paper, plastic, and metallic films.
This printing method is widely favored for its ability to handle high-speed production and its versatility in printing on different materials, making it a go-to method for packaging, labels, and other large-scale printing needs.
How Flexographic Printing Works
Flexo printing machines are designed with several key components that work together to produce high-quality prints. The primary parts include:
- Anilox roller: responsible for applying a consistent layer of ink onto the printing plate. It’s covered with tiny cells that hold the ink, ensuring the right amount is transferred.
- Plate cylinder: The flexible relief plate is mounted on this cylinder. As the cylinder rotates, the raised images on the plate come into contact with the substrate, transferring the ink to create the desired print.
- Impression cylinder: This cylinder presses the substrate against the plate cylinder, ensuring even pressure and proper ink transfer.
- Doctor blade: A thin blade that scrapes excess ink from the anilox roller, ensuring that only the right amount of ink is transferred to the plate.
Step-by-Step Process
- Preparation: This printing process begins with creating the flexible relief plates. The design is etched onto these plates, with raised areas representing the parts of the design that will receive ink.
- Inking: Ink is applied to the anilox roller, which then transfers it to the plate. The doctor blade removes any excess ink from the roller.
- Printing: The plate cylinder presses the inked plate onto the substrate, with the impression cylinder ensuring consistent pressure.
- Drying: After the ink is transferred, the printed substrate passes through a drying system to set the ink quickly.
Flexo printing: Pros and Cons
What make Flexographic printing a Game-Changing Technology
Flexographic printing stands out as a highly efficient and versatile printing method, making it a game-changer particularly for large-scale production.
1. High speed
Flexo printing is known for its rapid production capabilities. This method allows for continuous printing, making it ideal for high-volume projects like packaging and labels.
2. Versatility
One of the biggest advantages of flexographic printing is its ability to print on a wide range of materials, especially those used for making labels:
- Paper
- Plastics: Polypropylene (PP) and polyethylene (PE)
- Vinyl
- Metallic films
- Foil
- Shrink sleeves
Thus, the printed products of this printing method are suitable for various applications, from food packaging to industrial labels.
3. Low maintenance
Flexo printing machines have fewer moving parts compared to other printing methods, which means they require less maintenance. This not only reduces downtime but also lowers the overall cost of operation.
Drawbacks of Flexographic Printing
While flexographic printing offers many benefits, it also has some drawbacks that are important to consider:
1. Initial setup
One of the primary challenges of this printing is the initial setup cost. Creating the flexible relief plates can be expensive, especially for short print runs. Additionally, the time required to set up the printing plates can delay production.
2. Limited color reproduction
Flexographic printing can struggle with achieving very fine detail and smooth color gradients. Unlike digital or offset printing, flexo may face challenges in reproducing complex designs with multiple colors.
These limitations make flexo printing less suitable for projects that require high-resolution images or intricate color work. Also, it is less ideal for projects that need quick turnarounds.
Best Applications of Flexographic Printing
Flexographic printing is highly valued across various industries. Here are some of its best applications:
1. Flexible packaging
Its high speed and cost-effectiveness, combined with the ability to print on non-porous surfaces like plastic, make flexographic printing ideal for producing flexible packaging. It is widely used for printing on:
- Plastic bags
- Pouches
- Wrappers
2. Labels and Tags
The flexibility with substrates and ability to print on a wide range of materials, including paper and plastic, make flexo printing a popular choice for creating durable and high-quality labels. This printing method excels in producing labels and tags for bottles, cans, and other products
4. Corrugated boxes
Flexographic printing is the go-to method for printing directly onto corrugated boxes used in shipping and packaging. Its high efficiency and capability to handle thick, sturdy materials ensure that these boxes are not only functional but also visually appealing.
5. Mass-produced newspapers and magazines
For newspapers and magazines that need to be printed in large volumes, flexo printing offers high-speed production and cost-effectiveness. It allows publishers to meet tight deadlines while keeping production costs low.
6. Envelopes and stationery
Flexographic printing is also commonly used for printing envelopes and stationery. It’s economical for bulk printing and capable of handling various paper types, making it a reliable choice for businesses that need large quantities of printed materials.
Wrap it up
In conclusion, flexographic printing is a versatile and efficient method, ideal for high-speed, large-volume production. The printed results of this method is widely used across various industries, including flexible packaging, labels, tags, envelopes and more.
If you’re interested in learning more about other printing methods or have inquiries about printing-related issues, be sure to explore our blog page, which offers you various in-depth articles about different printing techniques.
FAQs
1. What are the main advantages of Flexographic printing?
Flexographic printing offers high-speed production, versatility in printing on a wide range of substrates, and cost-effectiveness for large-volume print runs. It’s also known for its durability and low maintenance needs.
2. What are the limitations of Flexographic printing?
The main limitations of flexographic printing include higher initial setup costs, particularly for short runs; and challenges with achieving fine details and color gradients compared to digital or offset printing.
3. What types of substrates can be used with Flexographic printing?
Flexographic printing can handle a variety of substrates, including paper, plastic, metallic films, and non-porous materials, making it ideal for diverse applications like packaging, labels, and more.
4. What should I consider when choosing flexo printing for my project?
When choosing flexo printing, consider factors such as the type of substrate, the volume of the print run, color requirements, and the budget for setup costs.
5. Are there any environmental benefits to using flexo printing?
Yes, flexographic printing can be environmentally friendly, especially when using water-based or UV-curable inks, which reduce harmful emissions and waste.
6. What is flexographic printing used for?
Flexographic printing is commonly used for producing flexible packaging, labels, corrugated boxes, mass-produced newspapers, magazines, envelopes, and stationery.