Pad Printing vs Screen Printing: A Comprehensive Comparison
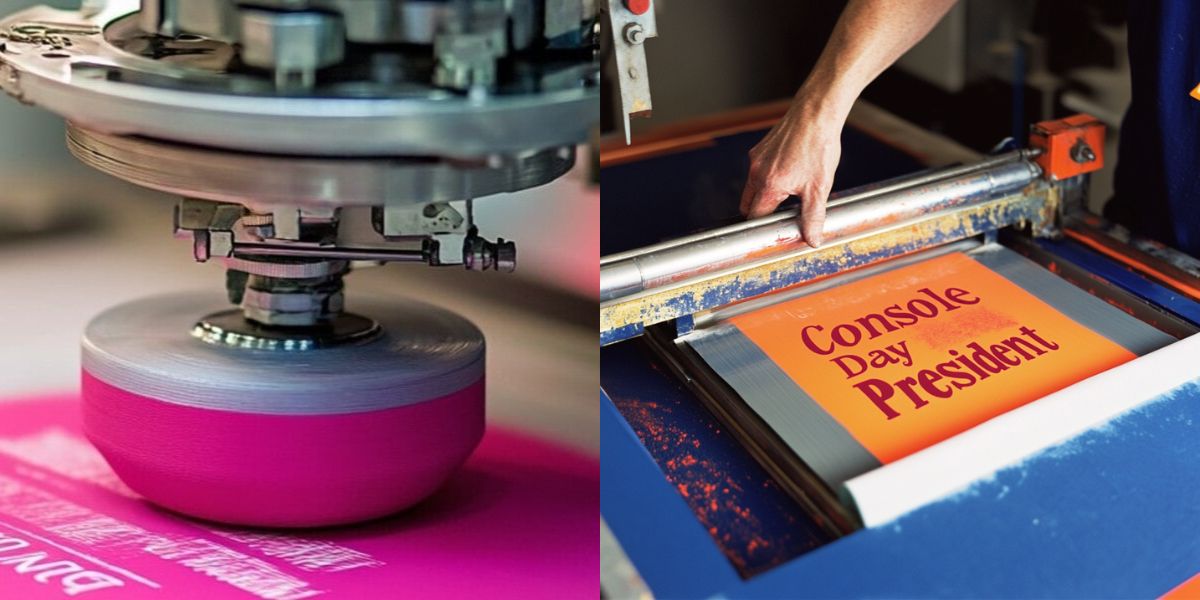
When finding a printing method to transfer designs onto various surfaces, many people face the choice between 2 popular methods: pad printing vs screen printing. Although both are versatile and offer high quality results, each technique offers distinct advantages, which is suited to specific types of projects.
Therefore, in this blog, CustomAny will explain about pad printing vs screen printing, and give a comprehensive comparison about their similarities and differences. Let’s explore so that you make an informed decision for your printing needs!
Understanding the Basics
What is Pad Printing?
Pad printing is widely used. It transfers a design or image onto a surface by stamping it. This process uses a silicone pad to transfer a 2D image onto a 3D object.
The silicone pad adapts to the object’s shape, then transfers the ink onto it. As a result of this flexibility, pad printing machines are highly effective for curved or irregular objects.
Consequently, this method is used to print on products in many industries, including:
- Medical items
- Automotive items
- Promotional items
- Electronic objects
- Sports equipment
- Appliances
- Toys
You may find this interesting: What Is Pad Printing? Everything You Need to Know
What is Screen Printing?
Screen printing, often referred to as silk screening, is a widely used technique that involves pushing ink through a mesh screen onto a surface to produce vivid and durable images.
The process starts with creating a stencil or screen that controls where the ink is applied to the substrate underneath. For multi-color and detailed designs, each color requires a separate screen.
This method is highly adaptable, making it suitable for a range of materials and surfaces, including:
- Textiles
- Paper
- Glass
- Plastics
- Metals
Related blog: Screen Printing Machine 101
Pad Printing vs Screen Printing: Similarities
Both pad printing vs screen printing are essential in various printing applications because they share the following similarities:
1. Multi-Color Printing
Firstly, both methods support multi-color printing. By utilizing separate plates or screens for each color, they can produce intricate, multi-colored designs with accuracy. This capability is crucial for projects that require detailed and vibrant visual elements.
2. Multiple material compatibility
Secondly, multiple material compatibility is a strength of pad printing vs screen printing. As mentioned above, both pad print vs screen print can handle a wide range of surfaces. This versatility allows them to be used across different industries, from promotional products to industrial components.
3. Precision and detail
Next, both pad printing vs screen printing are known for their precision and detail:
- Pad printing excels at transferring fine details onto curved or irregular surfaces
- Screen printing provides sharp, high-quality prints on flat surfaces.
4. Require equipment and setup
Both pad printing vs screen printing require specific equipment and settings. The process of preparing the necessary plates, pads, or screens involves careful planning and precision.
Pad Printing vs Screen Printing: Differences
Now you know what are the similarities of 2 printing methods: pad printing vs screen printing. However, it’s important to understand the differences between pad printing vs screen printing, especially when you want to make the best out of your prints.
Here is the comparison table so that you can shortly know the key differences between these 2 printing techniques:
Criteria | Pad Printing | Screen Printing |
Surface compatibility | Irregular and curved surfaces | Flat and slightly curved surfaces |
Print quality | Printing with high resolution, ideal for intricate designs | Suitable for bold designs, but might lack fine details |
Production volume | The production speed is slower, suitable for small to medium-sized runs | The production speed is faster, suitable for large volumes |
Setup time | Setup is more complex, each design requires metal plates | The setup is faster, but each color and design requires a screen |
Durability | Prints are durable, particularly on hard surfaces | Prints are durable, especially on textiles and flat items |
Cost | The cost is higher for large runs. It works better for small batches and complex surfaces | Large orders are cost-effective, and after setup there are lower costs per unit |
1. Surface compatibility
Pad printing
Pad printing excels in dealing with irregularly shaped or textured surfaces. This method uses a flexible silicone pad to transfer ink, allowing it to conform to complex shapes, such as:
- The curves of promotional items: pens, mugs, keychains,..
- Electronics
- Industrial parts
- …
The adaptability of the pad ensures precise and consistent application, making it the preferred choice for non-flat surfaces.
Screen printing
Screen printing is best suited for flat or slightly curved surfaces. This method uses a mesh screen to apply ink through a stencil, making it ideal for producing vibrant, high-quality prints on:
- T-shirts
- Posters
- Signs
Its efficiency lies in its ability to quickly cover large, flat areas with consistent results.
2. Print quality: detail, color, resolution
Pad printing
With pad printing, even challenging surfaces can be printed with fine details and sharp resolutions. The precision of the silicone pad ensures that intricate designs are transferred accurately.
However, its color application is generally limited to solid colors, as gradients and full-color images are harder to achieve.
Screen printing
Screen printing can greatly deliver vibrant colors and smooth gradients. The thickness of the ink layer allows for bold and bright designs, making it ideal for graphics that require strong visual impact.
However, while it can handle detailed designs, extremely fine details may be less sharp compared to pad printing.
3. Production volume
Pad printing
Pad printing is generally slower in terms of production speed. This method involves a multi-step process. Each print requires precise alignment, which can be time-consuming, especially for intricate designs or multicolor prints.
Therefore, this printing method is best suited for small to medium-sized runs.
Screen printing
The screen printing machine is ideal for large volume orders because it offers significantly faster production speeds. Once the screens are set up, processes become more efficient. Besides, the ability to print multiple items simultaneously further enhances efficiency.
4. Setup time
Pad printing
Setting up pad printing involves the creation of etched pad printing plates for each design and the preparation of pads. This complexity makes it less suitable for quick or one-off projects, as the initial setup is time-consuming.
Screen printing
Screen printing also requires setup, with screens needing to be created for each color and design. However, once the screens are ready, the process is straightforward and quick.
This makes it more efficient than pad printing for larger batches, reducing the overall production time.
5. Durability
Pad printing
Pad printing produces durable and long-lasting prints, particularly on non-flat surfaces. Once the ink is cured, it adheres strongly to the material, resisting wear and tear even on frequently handled items like buttons or electronics.
Screen printing
A screen machine also provides durable printing results, especially when used on textiles and flat surfaces. The screen printing ink is thick and adheres well, especially when heat-set.
Cost
Pad printing
Pad printing tends to be more expensive for large production runs due to the intricate setup and slower process. It becomes cost-effective only for smaller runs, especially when dealing with surfaces that are challenging for other printing methods.
Screen printing
Screen printing is highly cost-effective for large orders. In bulk production, setup costs are spread over many items, so it lowers the cost per item significantly.
This makes it a more economical choice for high-volume projects.
Pad Printing vs Screen Printing: When to Choose Each
Once having a deep understanding about pad printing vs screen printing, their similarities and differences, you must have made a decision for yourself. However, here are our conclusion for better help you give more firm decision:
Pad printing
Pad printing is ideal option when:
- You work with irregularly shaped items. Its flexible silicone pad allows it to transfer ink onto objects that other methods struggle to handle like electronics, medical devices, and promotional products.
- Pad printing excels in producing fine details, making it the go-to option for intricate designs.
- It’s also well-suited for small batches, where precision is more critical than speed, allowing for high-quality results on challenging surfaces.
Screen printing
On the other hand, screen printing is the better choice for:
- Large, flat items, like T-shirts, as well as posters, signs, and other flat surfaces.
- Products that require bold, vibrant designs. Its ability to produce bright, opaque colors makes it ideal for designs that need to stand out
- This method is highly efficient for high-volume orders, as the setup process is quick and the cost per unit decreases significantly with scale.
Last words
In summary, the choice between pad printing vs screen printing depends on your project’s specific requirements. Pad printing is the best option for intricate designs on irregularly shaped items, while screen printing excels with bold designs on large, flat surfaces and high-volume orders.
Furthermore, if you’re interested in learning more about other printing techniques, such as digital printing, offset printing, or sublimation printing, visit our website. We provide detailed articles to help you choose the perfect method for your next project.