Laminate stickers vs non laminate stickers: Find the Superior Choice for Your Needs
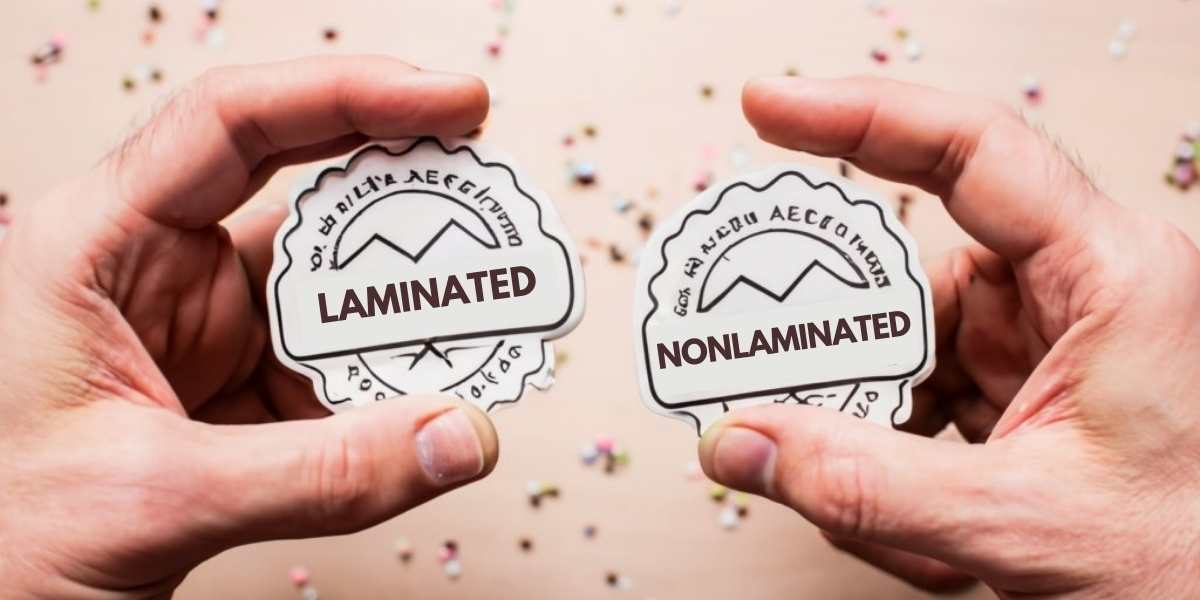
Stickers are the most practical and affordable method of spreading the message. Professionally designed and strategically positioned stickers make a strong statement. These stickers are more eye-catching than any newspaper ad and may be seen on automobiles, door jambs, and even notebooks. Thanks to the laminating process, laminate stickers have advantages over other printed media in terms of durability and cost.
However, some buyers are still wondering whether they need laminating stickers or not. In this article, CustomAny will give you the answer by telling you what laminate stickers are, the differences between laminate stickers and vs non laminate stickers, and how to laminate a sticker.
What is sticker lamination?
Definition
Lamination is a step of the production line in which an extra layer of material is added to a sticker to make it stronger, last longer, and look better. By laminating, we establish a permanent barrier to the sticker we’re protecting.
It is an additional coating that may be added to the top of manufactured stickers to make them more durable and extend their useful life by 1-3 years in harsh environments such as scratchy dirt and acid rain.
Also, it shields the sticker from the sun’s rays and keeps it dry and scratch-free.
Sticker finishes may be changed from glossy to matte by lamination.
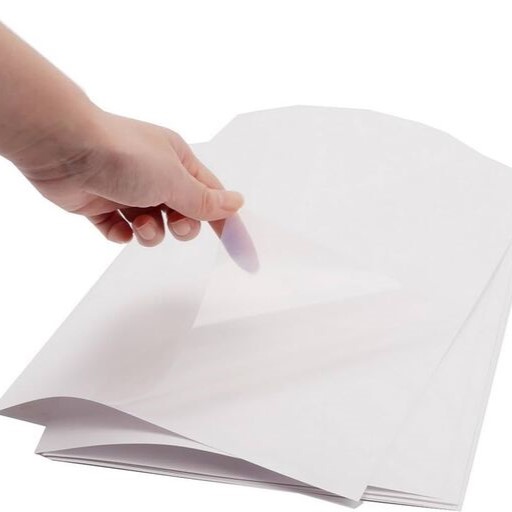
Types of Lamination
There are several different kinds of lamination, and although they all preserve your stickers, some may also provide a beautiful touch. With these options, you may choose the best laminate for stickers that suits your design needs.
You can alter the sticker’s feel with a different laminate, and some laminates provide additional functionality that isn’t available with other types of sticker protection.
Commonly, there are three main types of laminates for tickers.
- Gloss
- Matte
- Soft touch
Gloss
Gloss laminates are great for making laminating stickers shine. These laminates scatter light in all directions, giving your sticker a shiny finish that will catch the eye of passers-by.
Matte
If labels with a glossy finish aren’t your style, a matte laminate for stickers might give them a more understated look.
Thanks to the matte finish, your label’s surface won’t shine as much. But that doesn’t imply it will seem boring. As a result of the contrast between the matte texture and the more vibrant features and colors, these laminates may provide a deep, understated appearance.
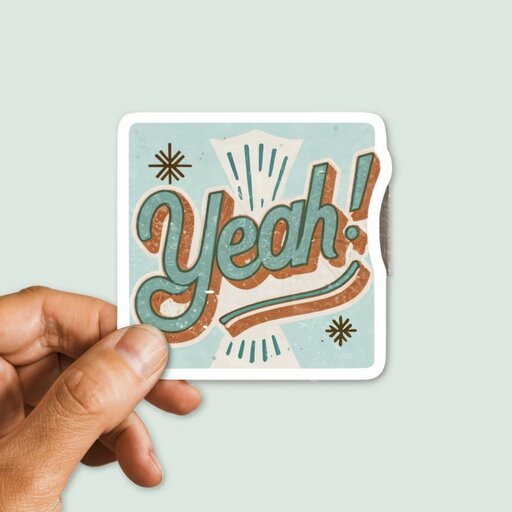
Soft touch
Using soft touch laminates on your labels gives them a tactile appeal that customers will appreciate. Laminated sticker paper has the appearance of matte lamination, and its texture is smooth and velvety. Soft touch laminates may be a key differentiator if you’re going for a luxurious feel.
Related article: “Glossy vs matte sticker: Which finish should you choose?“
Laminate stickers vs non laminate stickers
To help you get an idea of what you should choose between laminate stickers vs non laminate stickers, we will analyze some pros and cons of these two types of stickers.
Pros of the laminate stickers
1. Durability
Laminate is crucial for any professional-grade sticker work, even for a vehicle wrap. As a matter of fact, laminating stickers will be subjected to the elements such as rain, wind, and sunlight. The laminate layer provides extra bulk, which improves the product’s strength and stiffness and ultimately reinforces its framework.
It also helps to preserve the printed papers for longer. If you properly laminate an adhesive label, it can withstand being washed with water under high pressure and even harsh chemicals. Have confidence that even regular washing at a bike shop won’t ruin your decals.
Furthermore, laminate safeguards your stickers from harmful UV rays, allowing the colors and images to seem original for much longer.
2. Aesthetic enhancement
Laminating a product does more than just preserve it; it also improves the product’s aesthetics.
Although translucent, laminate enhances the sticker’s appearance by making the colors seem richer and more lively. And because it’s see-through, it doesn’t alter or damage the hues you started with.
It’s a cheap solution that greatly improves the quality of the sticker’s presentation.
3. Easier application
Laminate stickers provide more strength and rigidity, making them simpler to apply with less room for error. When properly laminated, laminated sticker paper does not wrinkle, crease, or fold.
Stickers whose adhesive has been damaged by being overstretched will peel at the edges. However, the laminating process increases the thickness of the finished product; stickers are protected from being overstretched and ripped during installation.
Cons of the laminated sticker:
1. Cost more
It is reasonable to assume that laminate sticker costs will rise along with the price of your sticker purchases because of the extra lamination material. However, the benefits, as discussed above, are well worth it in the long run.
2. Increase lead time
Certainly, the sticker printing shop’s lead time will increase if laminating procedures are required. This is why you need to think ahead when ordering laminated stickers and labels, particularly if you need custom die cuts or complex tracing for large quantities.
Do you need laminate stickers?
Any project using vinyl should seriously consider lamination. If your stickers will be shown outside and subjected to factors like rain, sun, and wind, lamination should be seriously considered. Vinyl’s structure may be further supported by lamination thanks to the added layer. Because of the increased thickness of the end product, the sticker is less likely to be damaged or overstretched.
When lamination is unnecessary
Lamination is recommended in the vast majority of circumstances; however, it is not always required. So, when comparing laminate stickers vs non laminate stickers, there are cases when you just need to use non laminated ones:
- Short-term sticker usage
For graphics that will be utilized for a short period, the laminating process is unnecessary. Most non-laminated stickers are durable enough to endure short-term use and UV exposure without affecting print quality. Sometimes they might go on for weeks without causing any noticeable damage.
- Stickers with high printing techniques
Lamination’s usefulness may be evaluated, to some extent, by the variety of printing techniques used. Ultraviolet (UV) printing is one such example. It’s a kind of digital printing that uses ultraviolet (UV) light to dry or cure ink nearly instantaneously when it makes contact with the printing materials. Since the print and color quality are already well preserved, lamination is unnecessary.
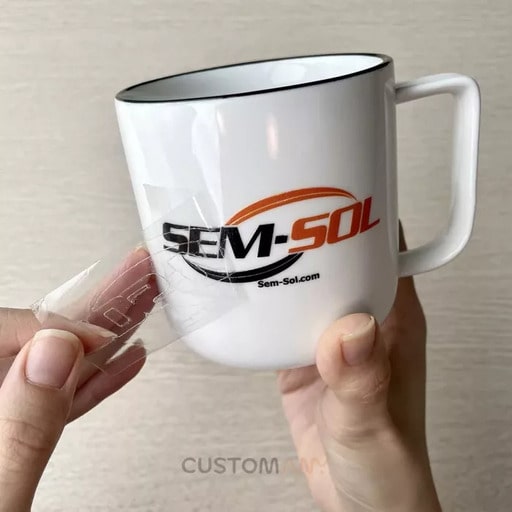
- Specific requirements of some shapes and materials
In the same approach, you may consider cut-stickers as another illustration. Stickers that are cut out don’t need to be laminated to make them more durable. This is because stickers that have been laminated may be too thick to easily apply to an uneven surface.
Digital printing techniques have come a long way and developed greatly over the years. Some printed materials may still benefit from lamination, although advancements in printing technology have made it unnecessary for many. Knowing the intended use and how you want to apply the stickers will help you determine what you need between laminate stickers vs non laminate stickers.
How to laminate stickers?
If you want to laminate a sticker, you have two options: cold laminate or hot laminate.
To complete a hot lamination, the laminate and the sticker paper are sent into a heat machine, where they are sealed using a high temperature. This will make sure that your sticker stays in place.
Hot lamination is suitable for bulk sticker production. In addition, this method requires skilled workers and high-quality machines to ensure no errors when using heat.
However, we think cold laminating is the better way to waterproof stickers. You risk having your designs warp if you laminate them using hot temperatures. Cold lamination is suitable for the DIY method with a small number of stickers.
Self-adhesive laminate is a common kind of cold laminate, as it is laminating without heat or machinery. A squeegee is all that’s needed to attach it to your best laminating sheets for stickers. To avoid scratching the sticker surface, we recommend using squeegees with a felt tip.
Conclusion
To ensure the longevity of a sticker product, turning them into laminate stickers is necessary. Stickers that will be exposed to the environment, wind, rain and cold should be laminated for maximum durability. It also makes the finishing protection more robust so that it isn’t pulled or overstretched during installation.
However, signs and stickers intended for a short-term display may not need lamination. You probably won’t set aside money specifically for laminating, but remember that your paper is still vulnerable to damage from tears, paper clips, pen caps, and more.
So, depending on our article about the advantages and disadvantages of laminate stickers vs non laminate stickers, as well as your personal requirement, choose the better one for you.