What’s the Ideal Labeling Adhesives for Your Product? 3 Factors to Consider
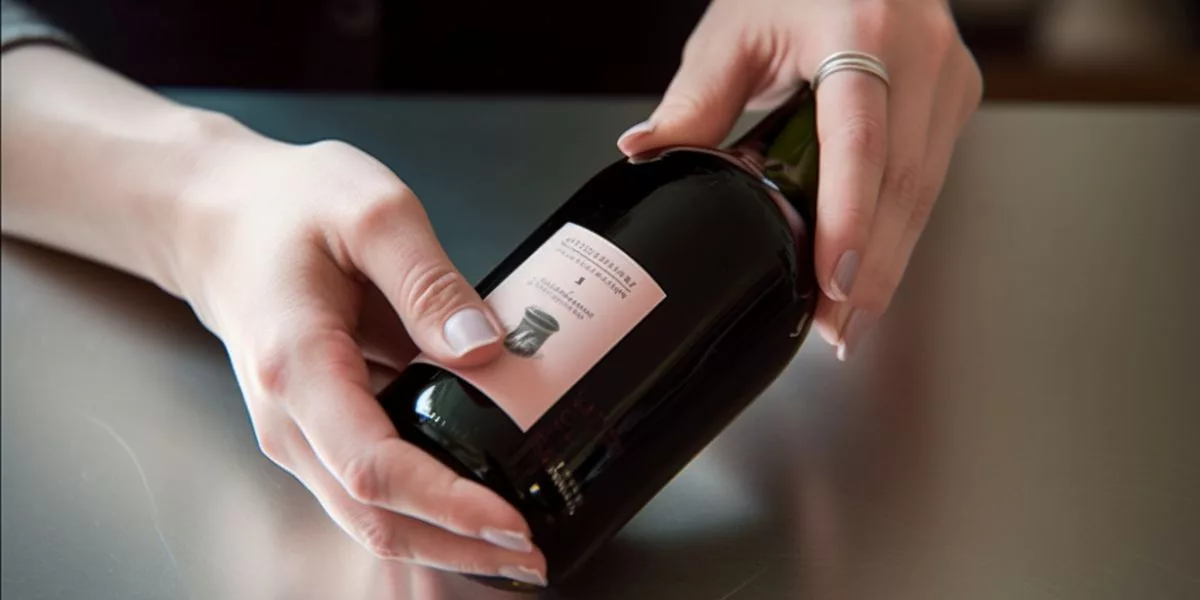
Are you looking for ideal labels for your product packaging but worrying that they are not sticking as securely as you’d like? Choosing the right labeling adhesives is crucial to ensure your greatly designed products’ labels fulfill all their functions and make a lasting impression.
Understanding this hardship, in this article, we’ll provide you the 3 key factors of the perfect label glue. From understanding product’s surface compatibility to assessing application requirements, we’ve got you covered. Let’s dive in and discover the adhesive secrets that will revolutionize your product packaging.
Importance of choosing the right label adhesive for product packaging
Choosing the right labeling adhesive for product packaging is important to ensure secure adhesion, which leads to the possibility of maintaining a professional appearance and providing essential information to customers.
Specifically, the glue for labels determines how well the labels stick to surfaces, ensuring a secure bond that prevents peeling or shifting. This is essential for labels to withstand environmental factors like moisture, temperature fluctuations, and exposure to chemicals, maintaining their appearance over time.
Additionally, it helps the label remain legible and functional throughout the product’s lifespan, serving their purpose effectively.
By selecting the appropriate label adhesive, you ensure a professional and reliable packaging solution for your products.
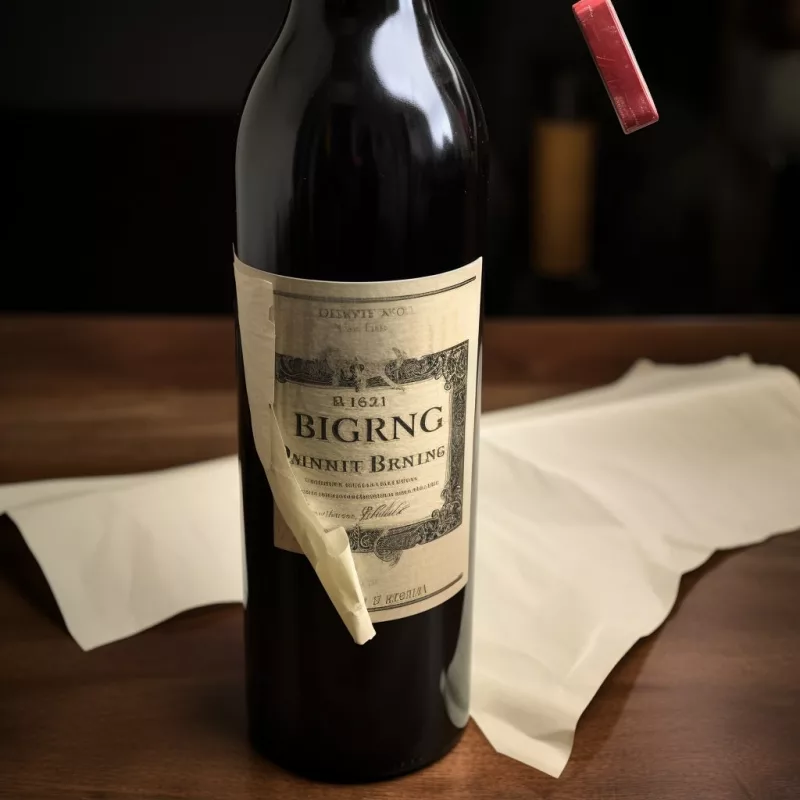
Label Adhesive Types
Let’s explore how many labeling adhesive types are available for you to choose from.
1. Permanent adhesive
Permanent adhesive is a type of labeling adhesive known for its strong and long-lasting adhesion. It is designed to create a secure bond between the label and the product packaging, ensuring that it remains firmly in place over an extended period.
The exact duration can vary depending on factors such as the surface type, environmental conditions, and the specific adhesive used. In general, permanent adhesive labels are intended to remain intact and securely bonded to the surface for the lifetime of the product.
Permanent adhesive is ideal for products that require labels that cannot be easily removed or repositioned. Products that benefit from permanent adhesive labels include:
- Bottled beverages and condiments: These products often face exposure to moisture, refrigeration, and handling, making permanent adhesive crucial for labels to remain intact and readable.
- Industrial equipment and machinery: Labels on machinery or equipment need to withstand harsh environments, including heat, vibrations, and chemicals, where permanent adhesive ensures labels stay firmly attached.
- Security seals and tamper-evident packaging: Products that require tamper-proof labels or security seals, such as pharmaceuticals, electronics, or high-value goods, benefit from the strong adhesive labels thanks to permanent adhesive.
If you attempt to remove a label that has been applied with permanent adhesive, it is challenging, which requires additional effort and may result in damage to the underlying surface.
2. Removable adhesive
True to its name, removable adhesive is a type of labeling adhesive that offers removal. It can be peeled off easily and cleanly without leaving residue or causing damage to the surface.
It is suitable for labels that are intended to be temporary or that may require repositioning, or that don’t require a permanent bond. Products that can benefit from removable labeling adhesive include:
- Food and beverage containers: Temporary labels for promotions, discounts, or limited-time offers can be easily applied and removed without leaving residue, ensuring a clean appearance.
- Retail and e-commerce packaging: Labels for temporary product information, special instructions, or promotional stickers can be conveniently applied and removed without damaging the packaging.
While removable adhesive (or peelable labels ) is designed to be easily removed, it should remain securely attached during the product’s normal usage. However, it is important to note that removable adhesive labels may not withstand long-term exposure to harsh conditions as effectively as permanent adhesive labels.
3. High-tack adhesive
High-tack adhesive is a type of labeling adhesive known for its extra strong adhesion. It is particularly effective on surfaces that are textured, irregular, or have low surface energy.
This labeling adhesive provides reliable adhesion on materials such as wood, metal, plastic, or fabric. It offers superior bonding strength, ensuring that labels stay securely attached in demanding environments.
With these key features, high-tack labeling adhesives are perfect for:
- Industrial equipment and machinery: Labels applied to machinery, equipment, or tools with rough or textured surfaces require high-tack adhesive to ensure long-lasting adhesion, even in harsh working conditions.
- Outdoor and automotive applications: Labels used in outdoor environments or on vehicles need high-tack adhesive to withstand exposure to extreme weather conditions, UV rays, and constant movement.
High-tack adhesive generally offers longer-lasting adhesion compared to removable adhesive but may have a shorter lifespan than permanent adhesive.
As with permanent adhesive, removing a label that has been applied with high-tack adhesive may require more effort and could potentially leave residue or damage the surface, particularly if the label has been in place for an extended period.
The above are the three basic types of labeling adhesives if we classify them based on adhesion. Additionally, there are special labeling adhesives that are specifically designed for some special application conditions, such as: freezer-grade adhesive, food-safe adhesive, ect.
3 Factors to Consider When Choosing Labeling Adhesives
Now that we’ve got in mind there’s basically 3 types of labeling adhesives we can choose from, let’s discover which type is suitable for your products. To do this, we need to consider 3 key factors as follow:
1. Product surface characteristics
When selecting label adhesive, it’s crucial to consider the characteristics of the product surface on which the label will be applied.
For smooth surfaces:
A smooth surface refers to a product’s surface that is even, flat, and lacks significant texture or roughness. It typically offers a sleek and uniform appearance without any prominent bumps, ridges, or irregularities.
Product containers with smooth surfaces include glass bottles, plastic containers, metal tins, glossy paper packaging, or smooth plastic packaging.
Permanent adhesive can be an excellent choice for smooth surfaces, as it provides strong adhesion and maintains label integrity. Besides, since these surfaces are easy to adhere to, you can also use removable labels if you’d like to. Both 2 types of labeling adhesive adhere well and provide a clean and professional look.
For textured surfaces:
A product with a textured surface has noticeable variations, irregularities, or patterns, creating a tactile or visual texture. These surfaces are not completely smooth and may have raised or indented areas, grooves, or roughness.
Embossed papers, textured plastics, fabrics, wood, or materials with a grainy appearance are examples of products with textured surfaces.
Applying labels to textured surfaces requires an adhesive that ensures proper adhesion and maintains label integrity on these uneven surfaces. So, high-tack labeling adhesive is recommended for this case.
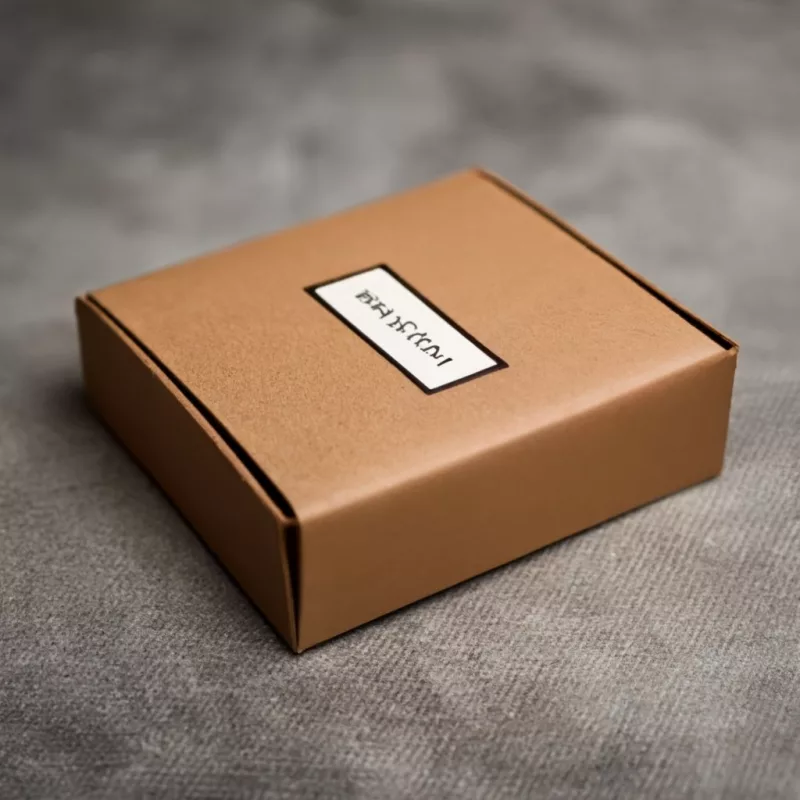
For porous materials:
Porous surfaces are those that have small openings or pores, allowing liquids or gasses to pass through or be absorbed, such as paper, cardboard, fabric, or certain types of wood.
Labels applied to porous materials may require an adhesive specifically designed for porous surfaces to ensure proper adhesion and minimize the risk of labels peeling or not sticking securely.
However, you should consider using removable adhesive if you prioritize easy removal without leaving residue on these uneven materials.
2. Temperature resistance
Temperature resistance is a crucial factor to consider when selecting label adhesive, particularly if your products will be exposed to extreme temperatures.
For high-temperature environments:
High-temperature environments are conditions where temperatures exceed normal room temperature ranges (above 74°F). Labeling applications that may withstand high-temperature include ovens, automotive engine compartments, outdoor environments with high sun exposure, ect.
A labeling adhesive suitable for such conditions is a permanent adhesive. This type of adhesive forms a strong and long-lasting bond, making it ideal for products that will be exposed to high temperatures throughout their lifecycle.
For low-temperature environments:
Low-temperature environments refer to conditions where temperatures are below normal room temperature ranges (below 68°F). Cold storage facilities, refrigerated transportation, frozen food sections in supermarkets, winter outdoor conditions, … are examples of low-temperature environments that product labels may be used in.
Vinyl labels with high-tack adhesive are suitable for this condition.
Besides, we recommend freezer-grade adhesive labels. This special labeling adhesive is specifically made for low-temperature environments or cold temperature applications. It maintains labels’ bonding strength and integrity even in freezer or refrigeration conditions.
Reminders:
- When producing materials to make product labels yourself, or ordering printed labels from a third party, always check the temperature resistance specifications provided by the supplier to ensure it meets the specific temperature requirements of your product’s environment.
- Conduct adhesive testing to ensure the selected adhesive performs well under the expected temperature conditions.
3. Label application requirements
Considering the label application requirements is crucial to ensure a seamless labeling process and meet your specific needs.
For hand application, we barely avoid making some mistakes in the process. The suitable labeling adhesives should offer a good balance of tackiness and adjustability, allowing for easy positioning and smooth application by hand, so we recommend using removable labeling adhesives.
Adhesives designed for machine application require specific characteristics such as consistent flow and compatibility with automated labeling equipment. In this case, permanent adhesives are efficient and accurate to use without causing disruptions in the labeling process.
However, both high-tack and removable labeling adhesives are good for auto application.
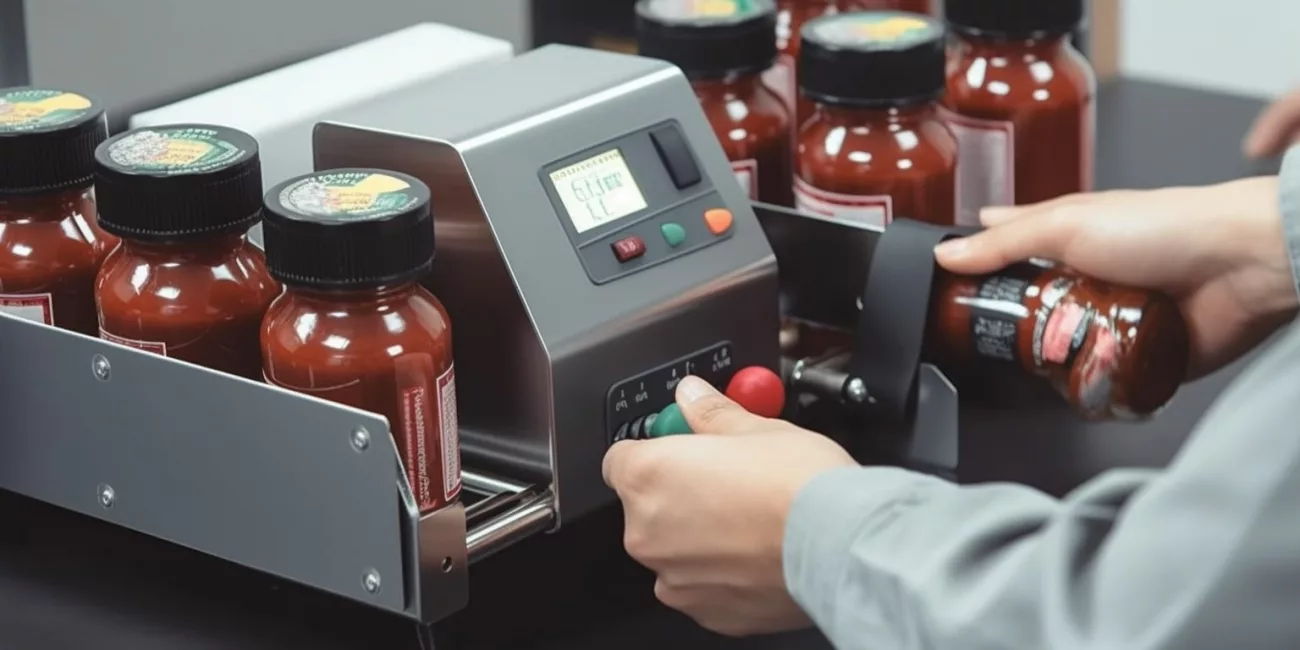
Balancing Adhesive Strength and Labels’s longevity
Finding the right adhesive means it meets your specific product needs and the expectations of your customers. So, striking a balance between adhesive strength and product longevity are crucial.
The adhesive should withstand environmental factors, such as temperature changes and exposure to moisture, while allowing a damage-free removal to maintain a great appearance for your product.
Conclusion
Selecting the right labeling adhesives is one of the key points which impact your product’s success in the market. By considering factors such as product surface characteristics, temperature resistance, and label application requirements as we discussed above, any business can ensure optimal label performance and customer satisfaction.
For a wide range of label adhesive options and further guidance on choosing the right adhesive for your specific needs, explore our website and check out our related articles on sticker and label selection tips.